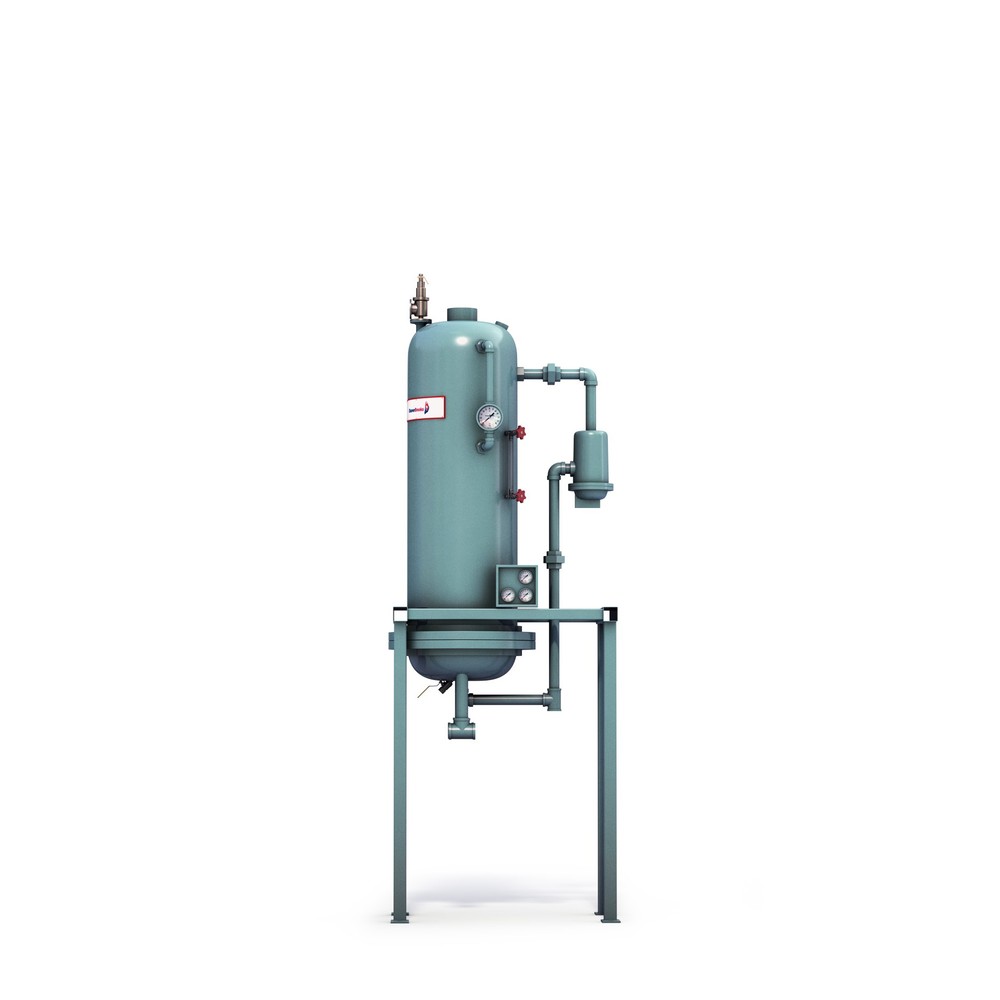
- For steam applications
- Captures waste heat from blowdown process
- Preheats cold makeup water
- Up to 22 gpm blowdown water
- Up to 180 gpm makeup water
- Efficient baffling separates the dirty blowdown water from the clean steam
- Transfers the remaining heat normally lost during blowdown to the cold makeup water as it flows to the feedwater heater
- Consists of an ASME-approved and stamped flash tank and a blowdown heat exchanger
- Compact, low-cost alternative to the shell and tube design
- Heat recovered as flashed steam
In addition to the heat recovered as flashed steam, the heat exchanger will transfer the remaining heat normally lost during blowdown to the cold makeup water as it flows to the feedwater heater. The systems quickly pay for themselves with fuel savings resulting from using heat that would otherwise be wasted. The model AHR is a coil-type, flash tank heat exchanger. It is a compact, low-cost alternative to the shell and tube design, while still offering waste heat recovery to pre-heat make-up water, reducing operating costs for the system.
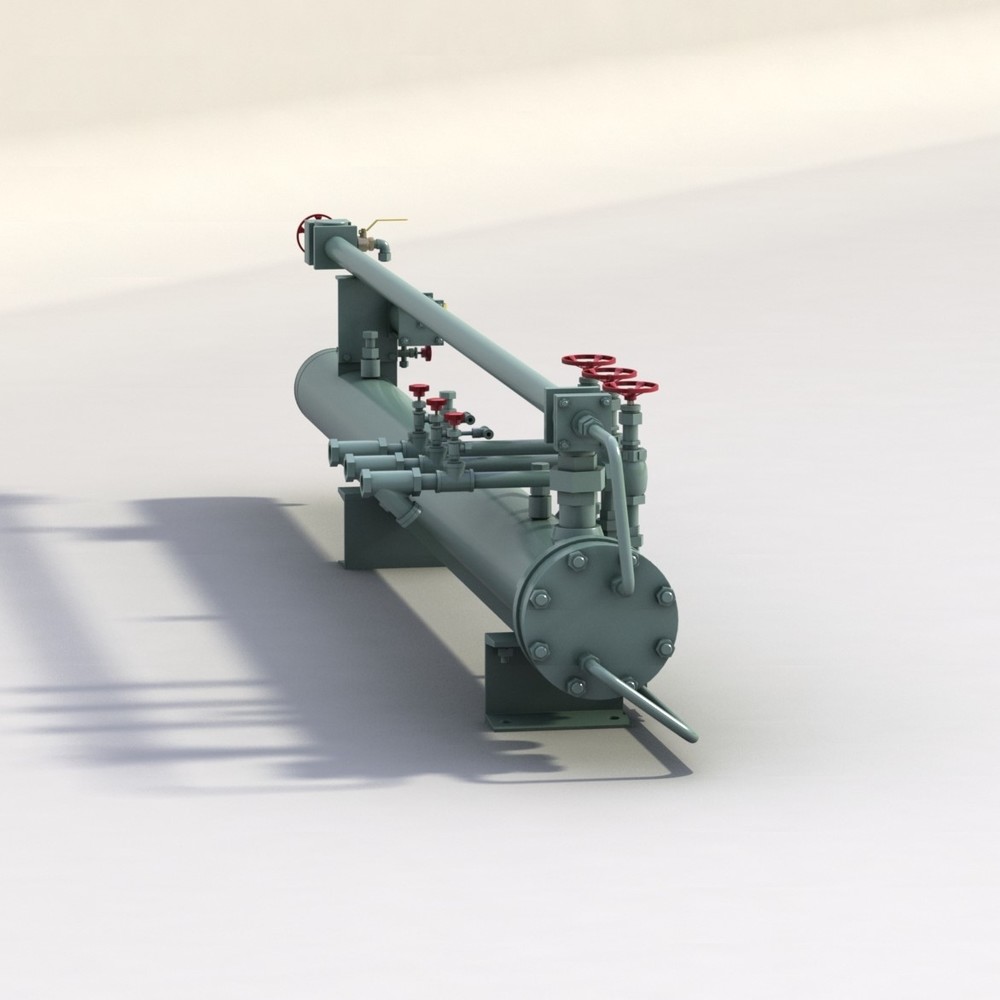
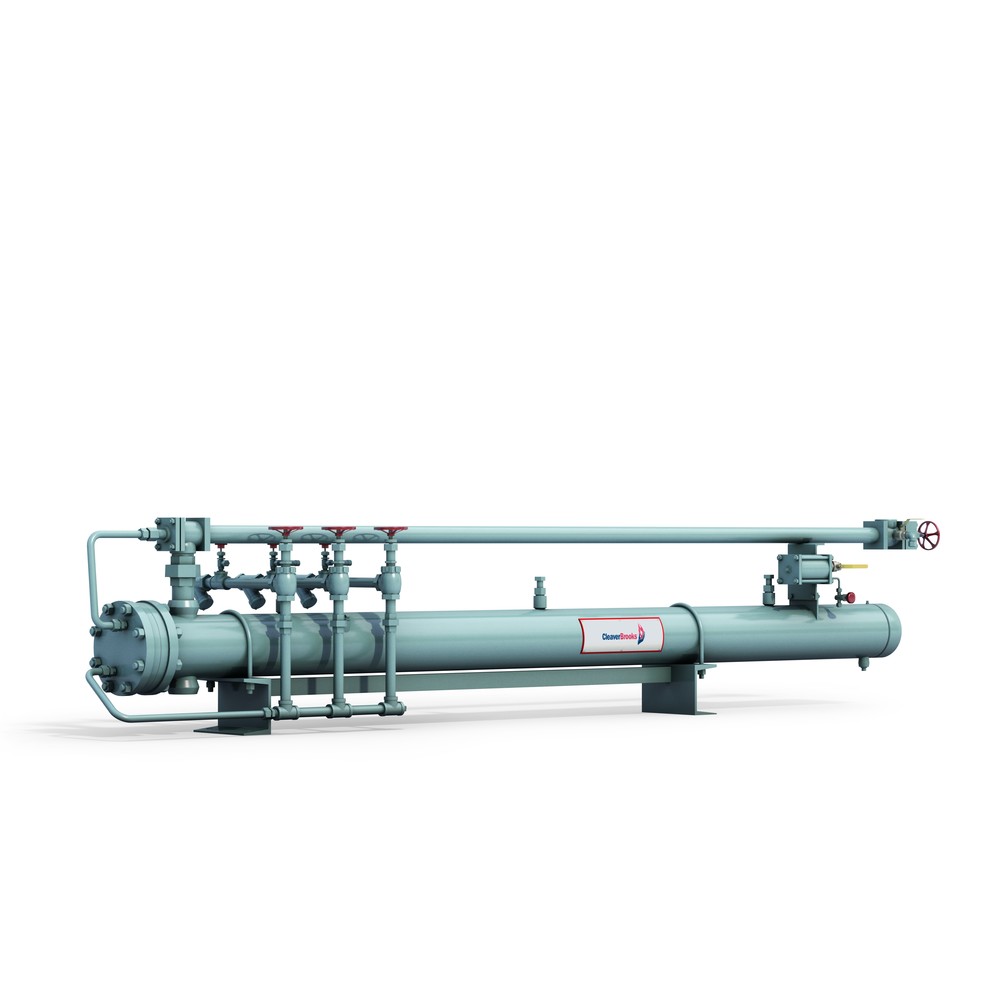
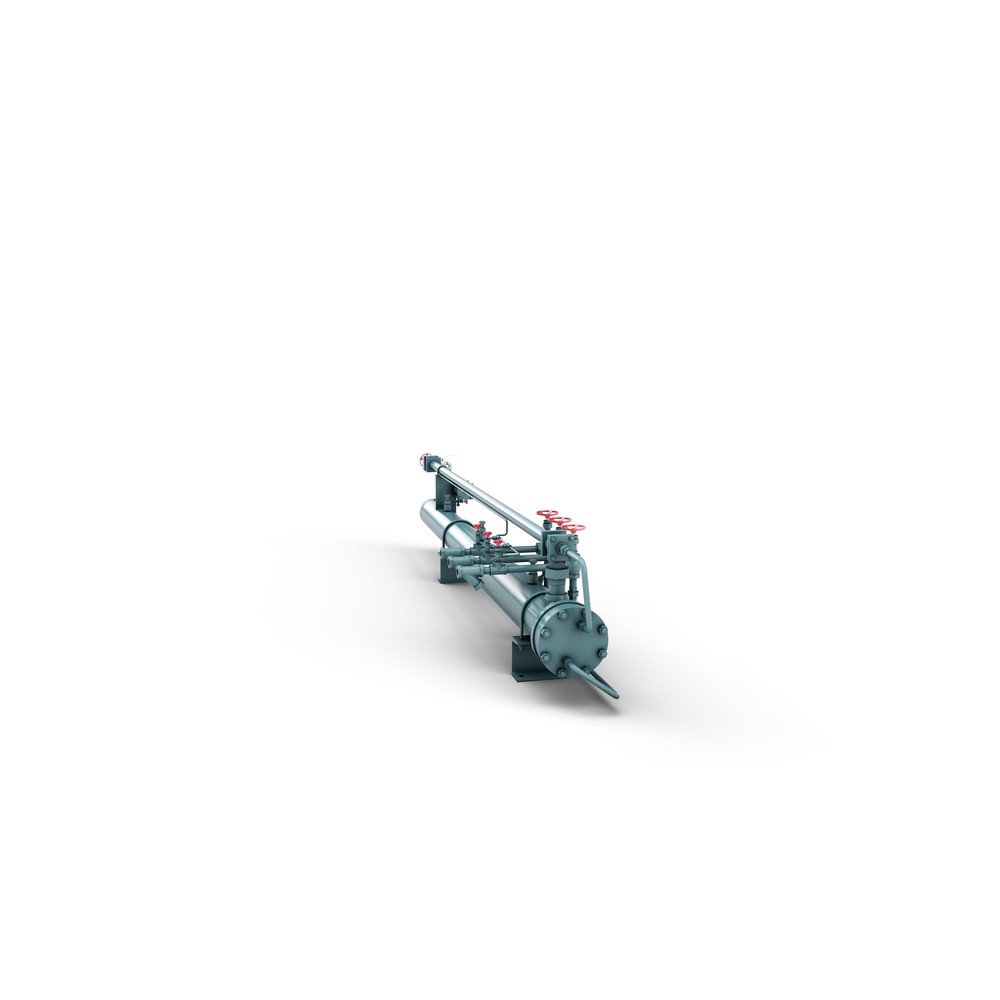
- For steam applications
- Captures waste heat from blowdown process
- Maintains desired level of total dissolved solids (TDS)
- Up to 22 gpm blowdown water
- Up to 180 gpm makeup water
- Automatically controls surface blowdown flow to maintain desired concentration of dissolved solids within the boiler
- Compact size for convenient placement
- Transfers the blowdown heat to the makeup, thereby decreasing fuel costs; nearly 100% efficiency at all operating points
- Saves chemical costs by reducing blowdown
- Recovers 90% of energy normally lost
The BDHR automatically controls the surface blowdown to maintain the desired level of total dissolved solids (TDS) in the boiler, reducing the amount of blowdown to a minimum. It also recovers the heat from the high-temperature blowdown and transfers it to the incoming cold makeup water, maximizing boiler efficiency. The blowdown heat recovery system will usually result in a payback in a few short months from fuel savings alone. Continuous boiler surface blowdown heat recovery (BDHR) is the most effective method of purging destructive solids from any steam boiler system, while also using the energy from the heated blowdown water to pre-heat the make-up water.
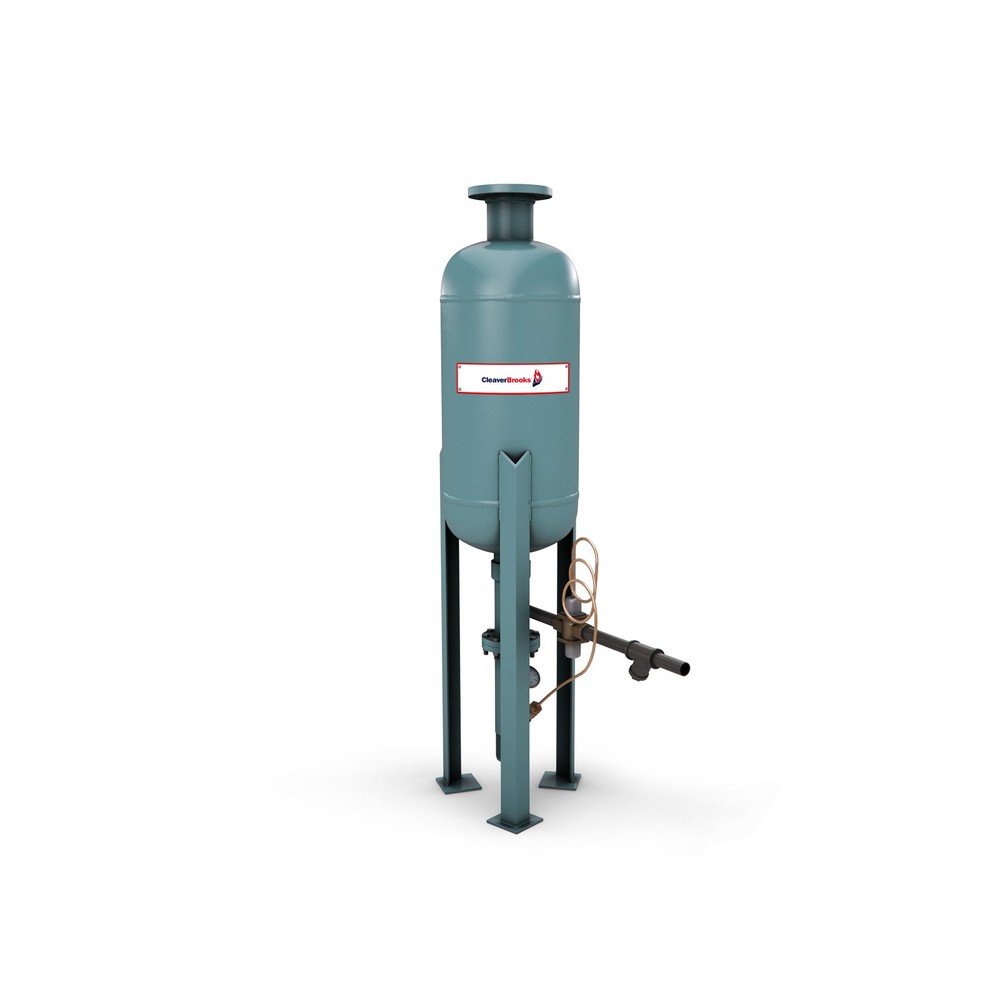
- Blowdown prevents buildup of harmful solids in steam boilers
- Blowdown helps maintain boiler water level safety controls
- Built-in Aftercooler protects wastewater disposal systems
- Compact Blowdown Separators — ASME Section VIII 250 psig tank design
- Blowoff Tanks for specific applications and ASME code requirement
Cleaver-Brooks model BDS blowdown separators and model BDT tanks use a safe, proven, economical flash purification process for facilitating blowdown effectiveness and disposal.
- Safe, economical method to separate steam and water from boiler blow-off and high temperature condensate
- Flash purification process safely vents clean steam to atmosphere
- Reduces drain water temperature to meet state and local requirements
- Quiet design, with noise levels below 90 dBA
- Stainless steel striking plate extends separator life
- Tangential inlet and high velocities promote cyclonic separation of steam and water
- Self-draining, self-drying design
- Proven performance, durable design, longer life
- ASME “U” and “UM” stamp available
- Available for any boiler capacity
- Tank designs up to 1600 psig
Model BDS blowdown separators offer an effective and compact solution to safely dispose of boiler blowdown and other high temperature process streams, including deaerator overflow or high temperature waste condensate from steam traps or pressure relief.
Model BDT blow-off tanks allow boiler blowdown to accumulate in a larger tank and cool, mixing with the next blowdown and thereby reducing the need for additional cooling water. All model BDT blow-off tanks are sized and designed according to ASME Section VIII and National Board specifications.
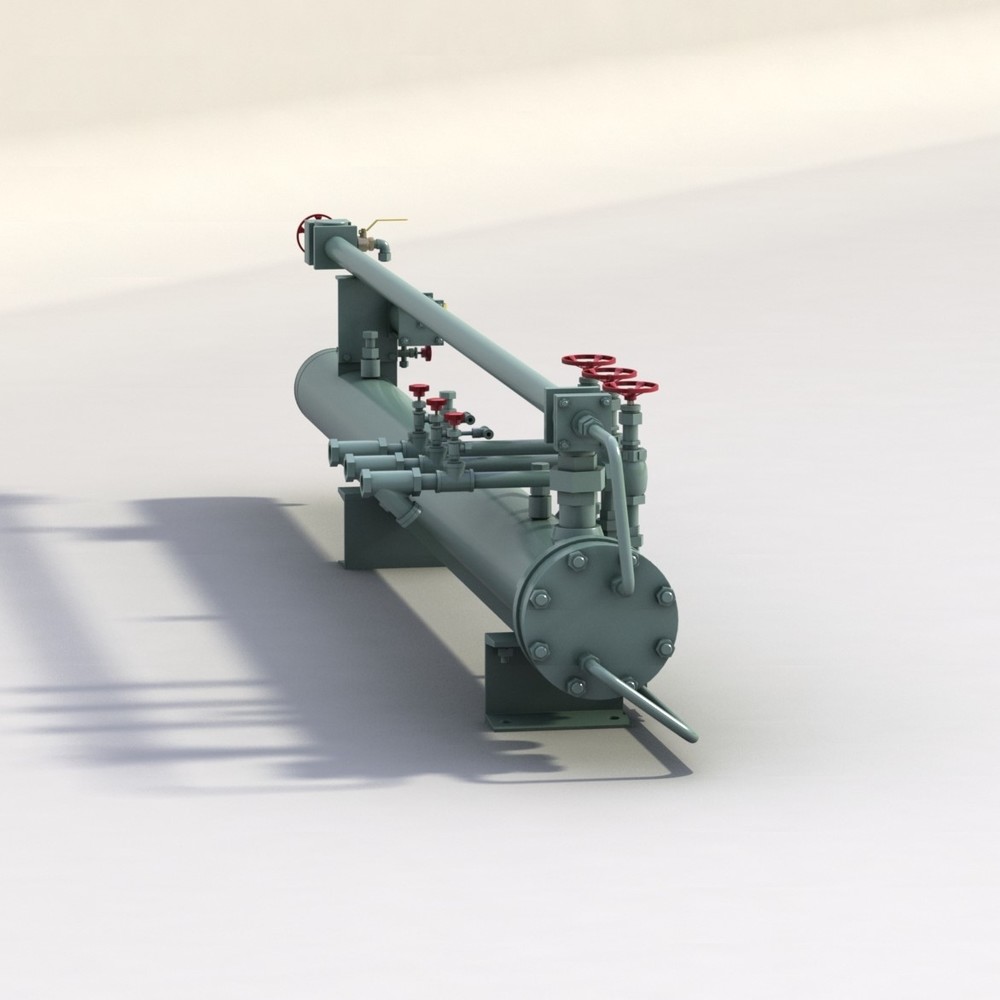
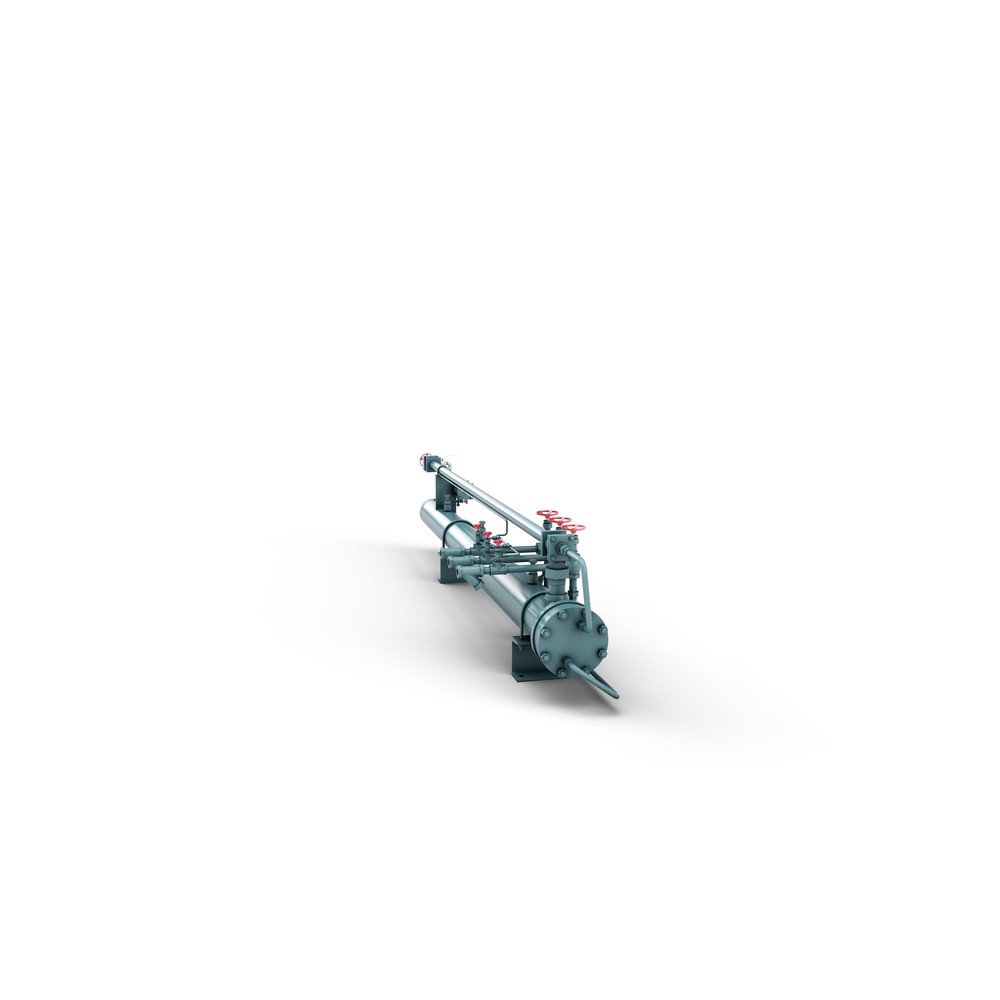
- For steam applications
- Captures waste heat from blowdown process
- Maintains desired level of total dissolved solids (TDS)
- Up to 22 gpm blowdown water
- Up to 180 gpm makeup water
- Automatically controls surface blowdown flow to maintain desired concentration of dissolved solids within the boiler
- Compact size for convenient placement
- Transfers the blowdown heat to the makeup, thereby decreasing fuel costs; nearly 100% efficiency at all operating points
- Saves chemical costs by reducing blowdown
- Recovers 90% of energy normally lost
The BDHR automatically controls the surface blowdown to maintain the desired level of total dissolved solids (TDS) in the boiler, reducing the amount of blowdown to a minimum. It also recovers the heat from the high-temperature blowdown and transfers it to the incoming cold makeup water, maximizing boiler efficiency. The blowdown heat recovery system will usually result in a payback in a few short months from fuel savings alone. Continuous boiler surface blowdown heat recovery (BDHR) is the most effective method of purging destructive solids from any steam boiler system, while also using the energy from the heated blowdown water to pre-heat the make-up water.
- Blowdown prevents buildup of harmful solids in steam boilers
- Blowdown helps maintain boiler water level safety controls
- Built-in Aftercooler protects wastewater disposal systems
- Compact Blowdown Separators — ASME Section VIII 250 psig tank design
- Blowoff Tanks for specific applications and ASME code requirement
Cleaver-Brooks model BDS blowdown separators and model BDT tanks use a safe, proven, economical flash purification process for facilitating blowdown effectiveness and disposal.
- Safe, economical method to separate steam and water from boiler blow-off and high temperature condensate
- Flash purification process safely vents clean steam to atmosphere
- Reduces drain water temperature to meet state and local requirements
- Quiet design, with noise levels below 90 dBA
- Stainless steel striking plate extends separator life
- Tangential inlet and high velocities promote cyclonic separation of steam and water
- Self-draining, self-drying design
- Proven performance, durable design, longer life
- ASME “U” and “UM” stamp available
- Available for any boiler capacity
- Tank designs up to 1600 psig
Model BDS blowdown separators offer an effective and compact solution to safely dispose of boiler blowdown and other high temperature process streams, including deaerator overflow or high temperature waste condensate from steam traps or pressure relief.
Model BDT blow-off tanks allow boiler blowdown to accumulate in a larger tank and cool, mixing with the next blowdown and thereby reducing the need for additional cooling water. All model BDT blow-off tanks are sized and designed according to ASME Section VIII and National Board specifications.
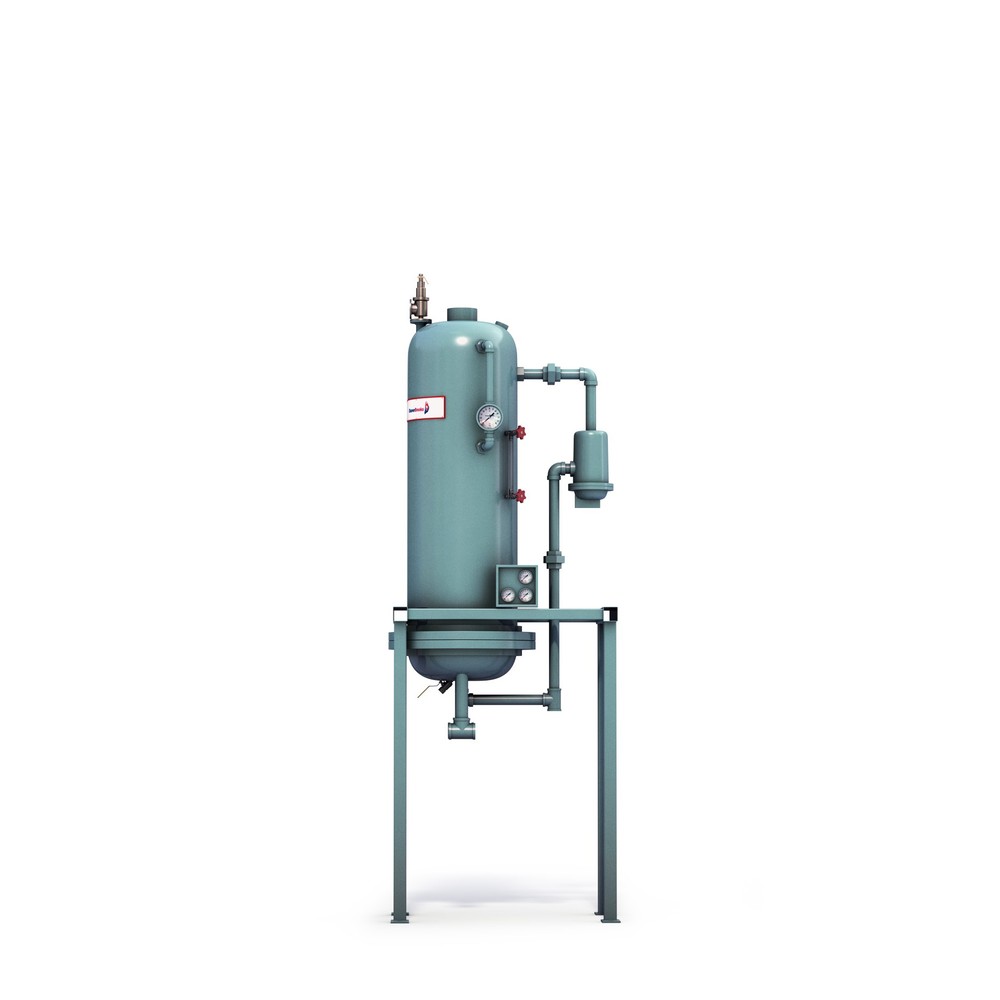
- For steam applications
- Captures waste heat from blowdown process
- Preheats cold makeup water
- Up to 22 gpm blowdown water
- Up to 180 gpm makeup water
- Efficient baffling separates the dirty blowdown water from the clean steam
- Transfers the remaining heat normally lost during blowdown to the cold makeup water as it flows to the feedwater heater
- Consists of an ASME-approved and stamped flash tank and a blowdown heat exchanger
- Compact, low-cost alternative to the shell and tube design
- Heat recovered as flashed steam
In addition to the heat recovered as flashed steam, the heat exchanger will transfer the remaining heat normally lost during blowdown to the cold makeup water as it flows to the feedwater heater. The systems quickly pay for themselves with fuel savings resulting from using heat that would otherwise be wasted. The model AHR is a coil-type, flash tank heat exchanger. It is a compact, low-cost alternative to the shell and tube design, while still offering waste heat recovery to pre-heat make-up water, reducing operating costs for the system.
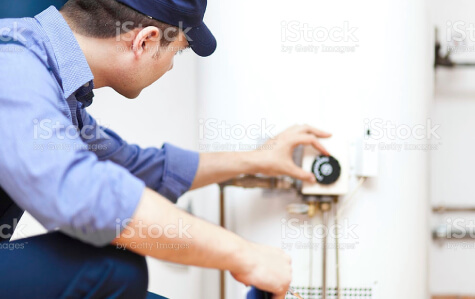
Watertube Boilers
Optimal versatility in a highly efficient, compact unit.
- FLX
- FLX PM
- M5
- M5M
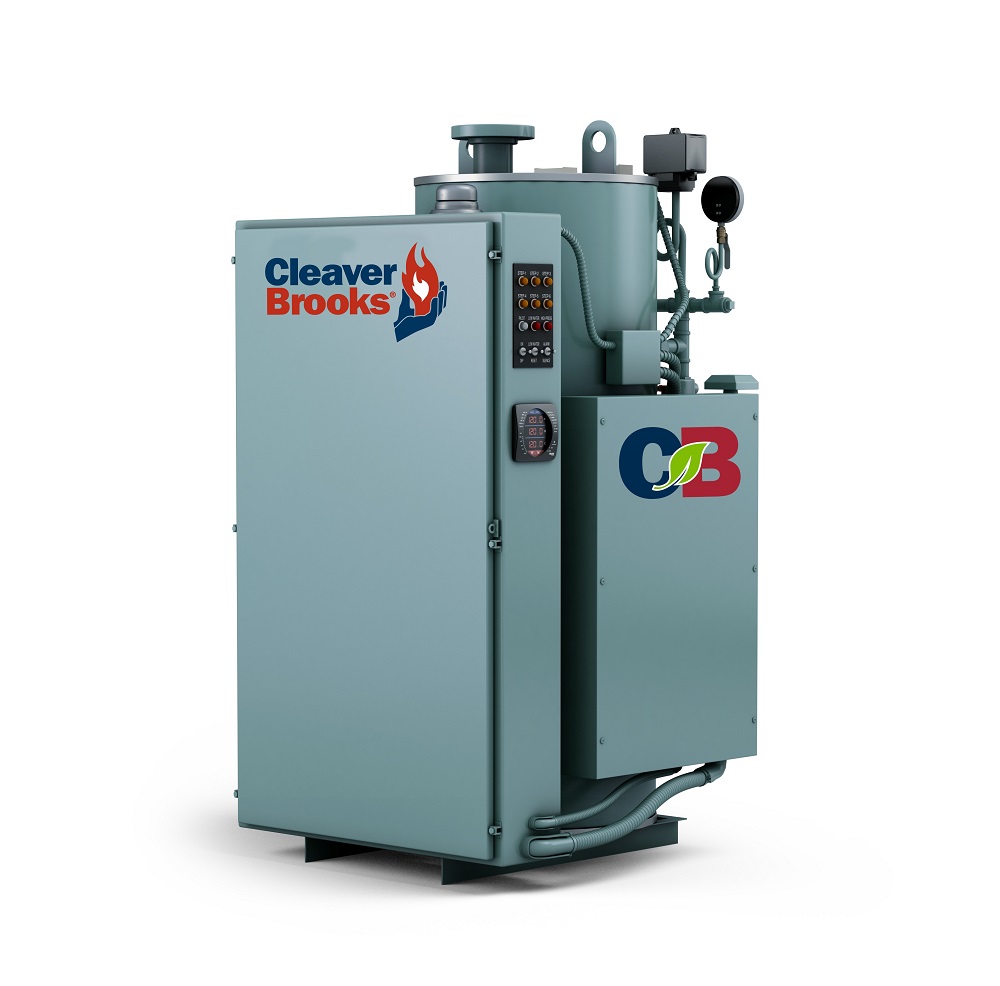
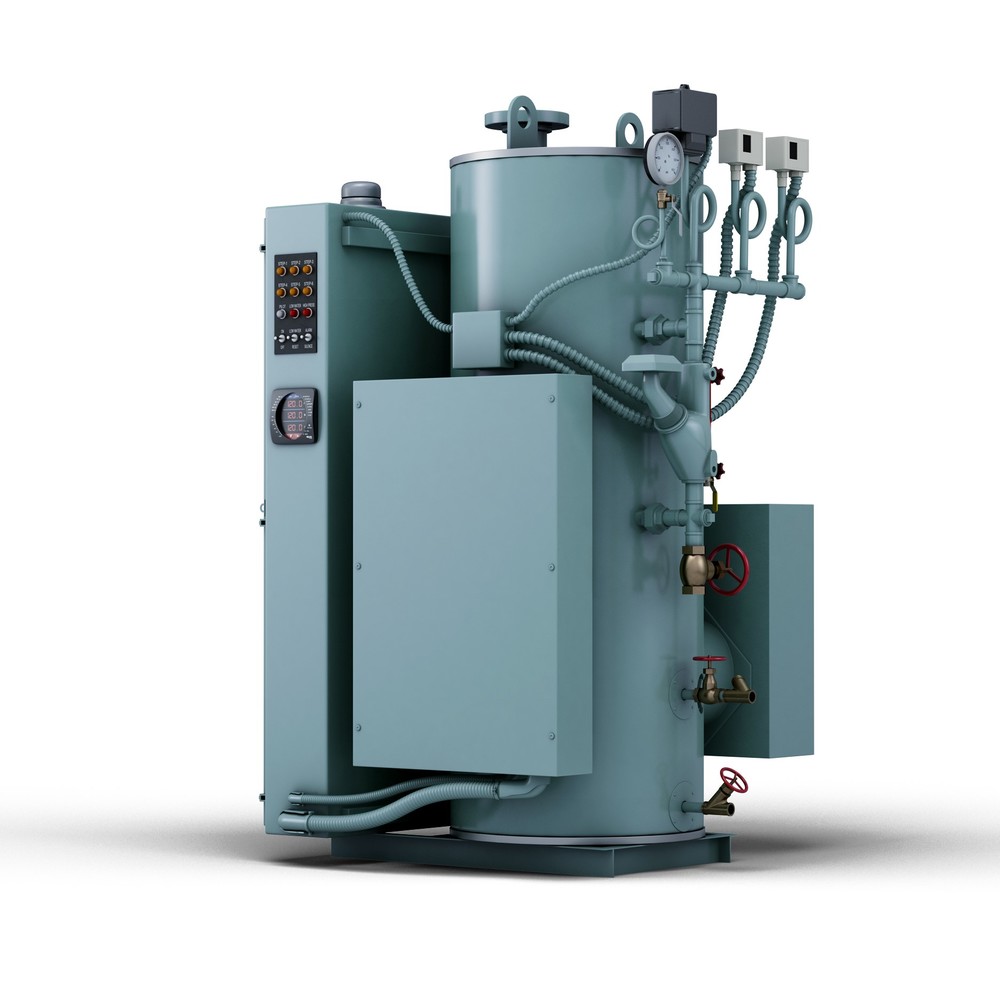
The Cleaver-Brooks Model S is an immersion-element steam electric boiler with a vertical, insulated vessel. This boiler is designed for the heavy-duty, continuous demand of commercial and industrial applications. Available in vessel sizes ranging from 12″ to 48″ diameter with an output spanning 12 kW to 2,250 kW. A typical Model S boiler system includes operating controls, elements, fuses, contactors, safety valve, and instrumentation.
- Electric vertical steam boiler
- 12 to 2250 KW – up to 7,875 lb/hr
- Up to 600V
- 15, 150, 200 & 250 psig
- No site emissions
- Compact design and smaller footprint
- No site emissions
- Quiet operation
- Nearly 100% efficiency at all operating points
- Ease of maintenance with reduced complexity/number of moving parts
- All units are fully packaged and ready for installation
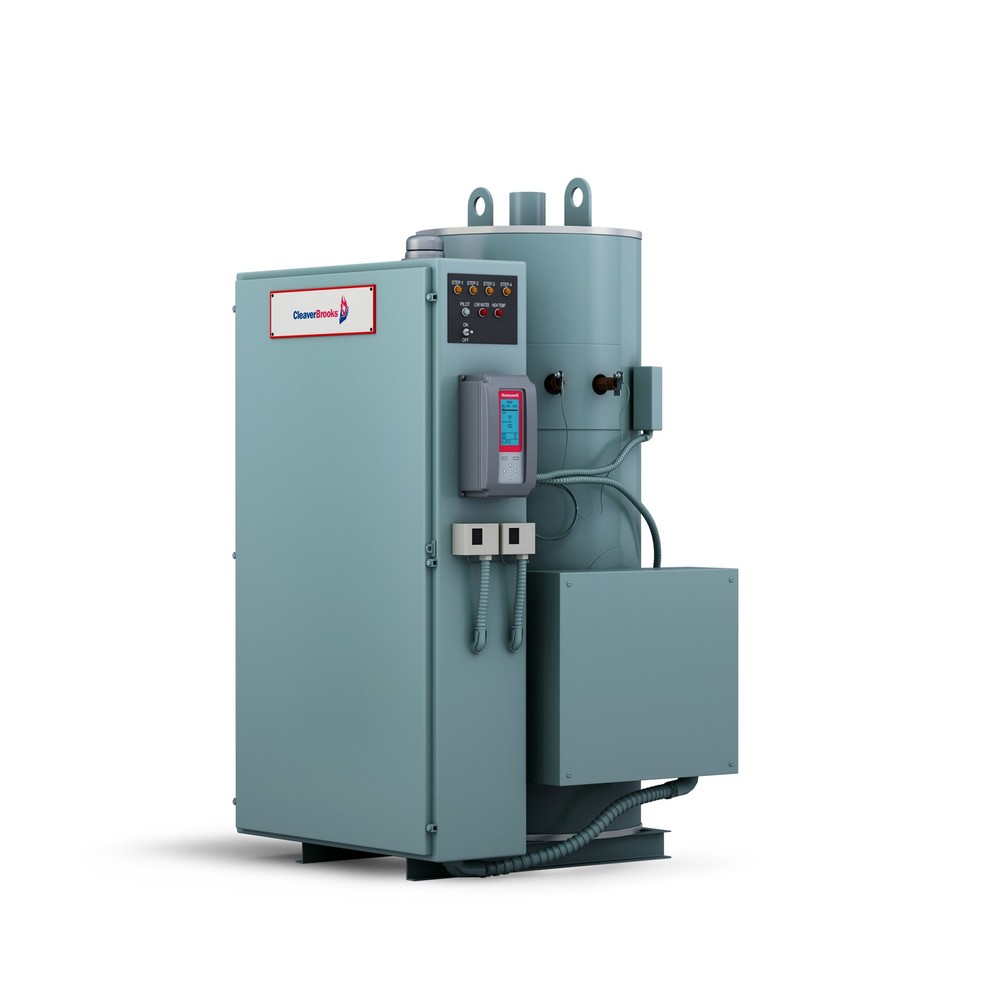
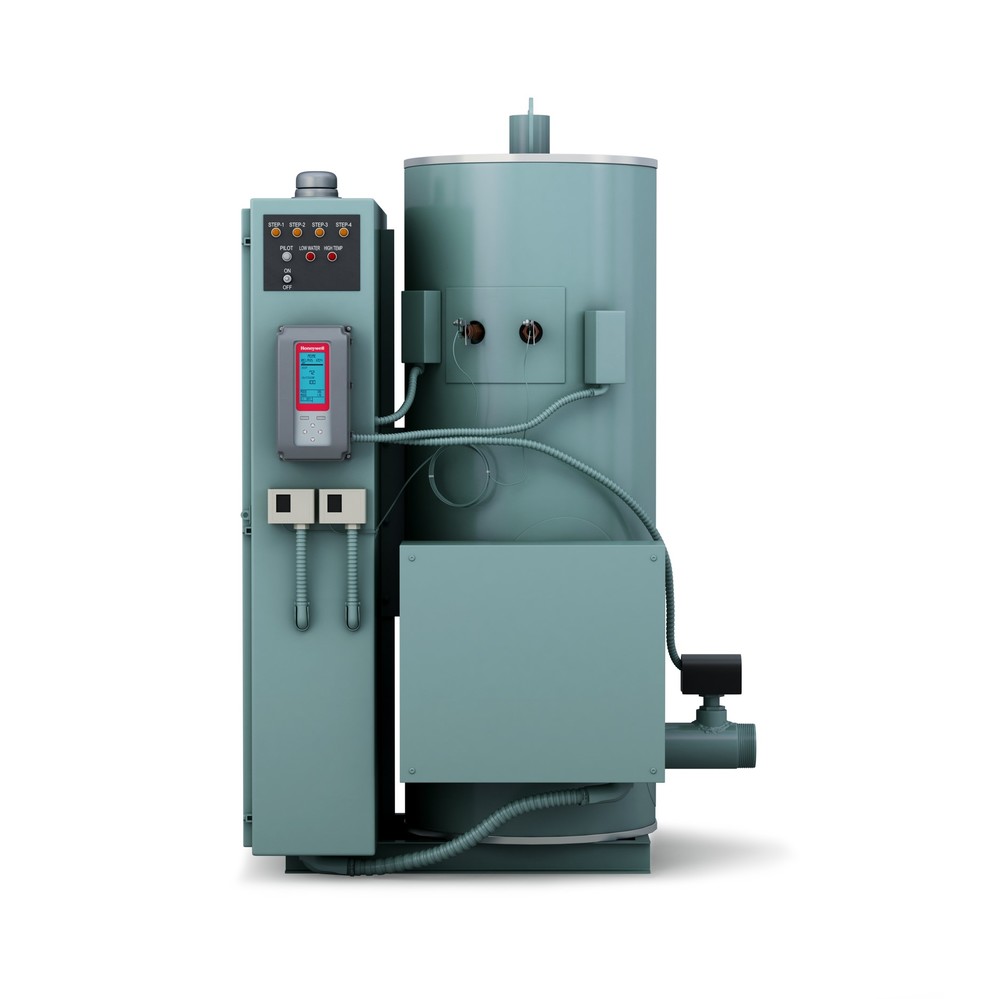
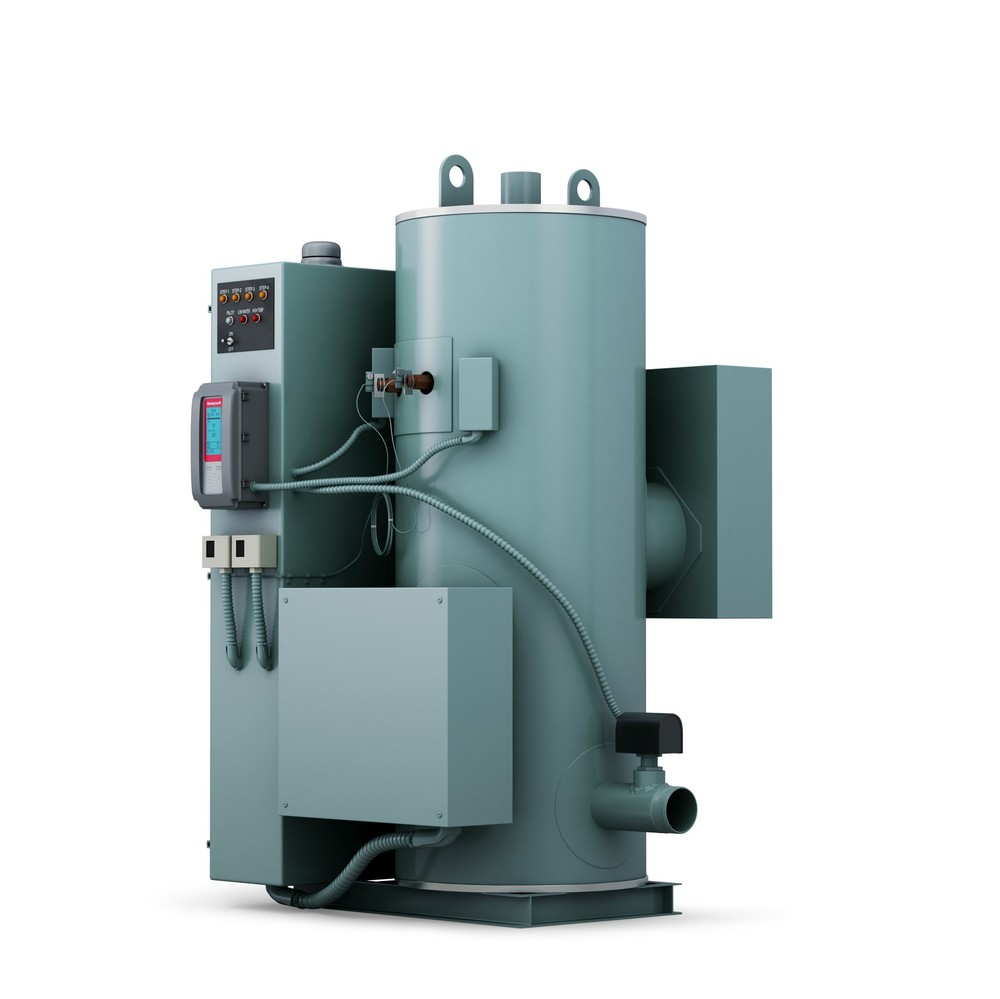
The Cleaver-Brooks Model WB is an immersion-element hot water boiler with a vertical, insulated vessel. This boiler is designed for the heavy-duty, continuous demand of commercial and industrial applications. Vessel sizes range from 12″ to 42″ diameter with an output spanning 12 kW to 3,360 kW. A typical Model WB boiler system includes operating controls, elements, fuses, contactors, safety valve, and instrumentation.
- Electric hot water boiler
- 12 to 3360 kW, up to 11.5 million Btu/hr
- Up to 600V
- 160, 200 & 250 psig
- No site emissions
- Compact design and smaller footprint
- No site emissions
- Quiet operation with virtually no noise emissions
- Nearly 100% efficiency at all operating points
- Ease of maintenance with reduced complexity/number of moving parts
- All units are fully packaged and ready for installation
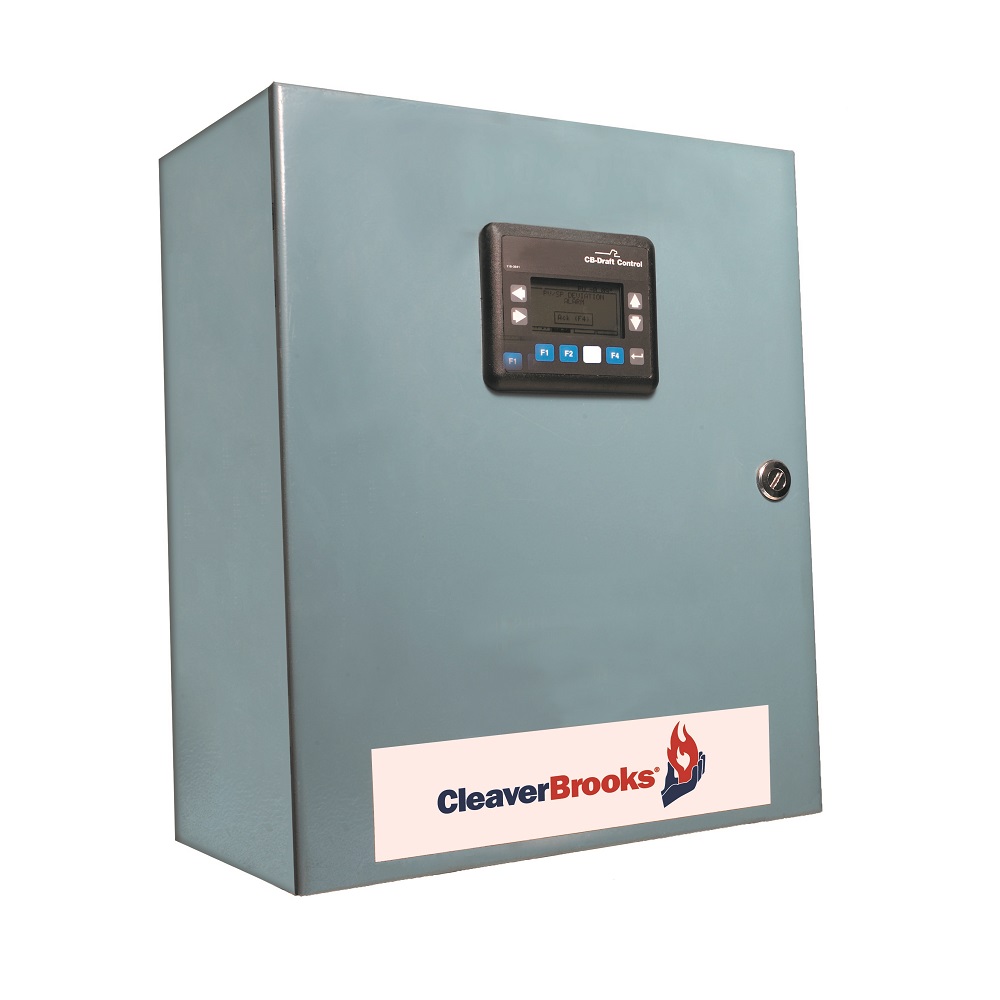
- Stand-alone stack Draft Control
- Steam or hot water applications
- Precise control
- Easy to set up
- Works with various size damper assemblies
- Precise draft control
The Cleaver-Brooks Accu-Draft is a stand-alone, stack draft control system designed to maintain stack draft on set point throughout the firing range of the boiler. Can be used on new equipment or applied to existing equipment as a field retrofit. The C-B Accu-Draft works with various C-B damper assemblies that include a low draft switch, draft transmitter, and damper actuator. The HMI included makes the C-B Accu-Draft’s operation and setup easy and operator-friendly. Other customized solutions are available to meet other more sophisticated installations.
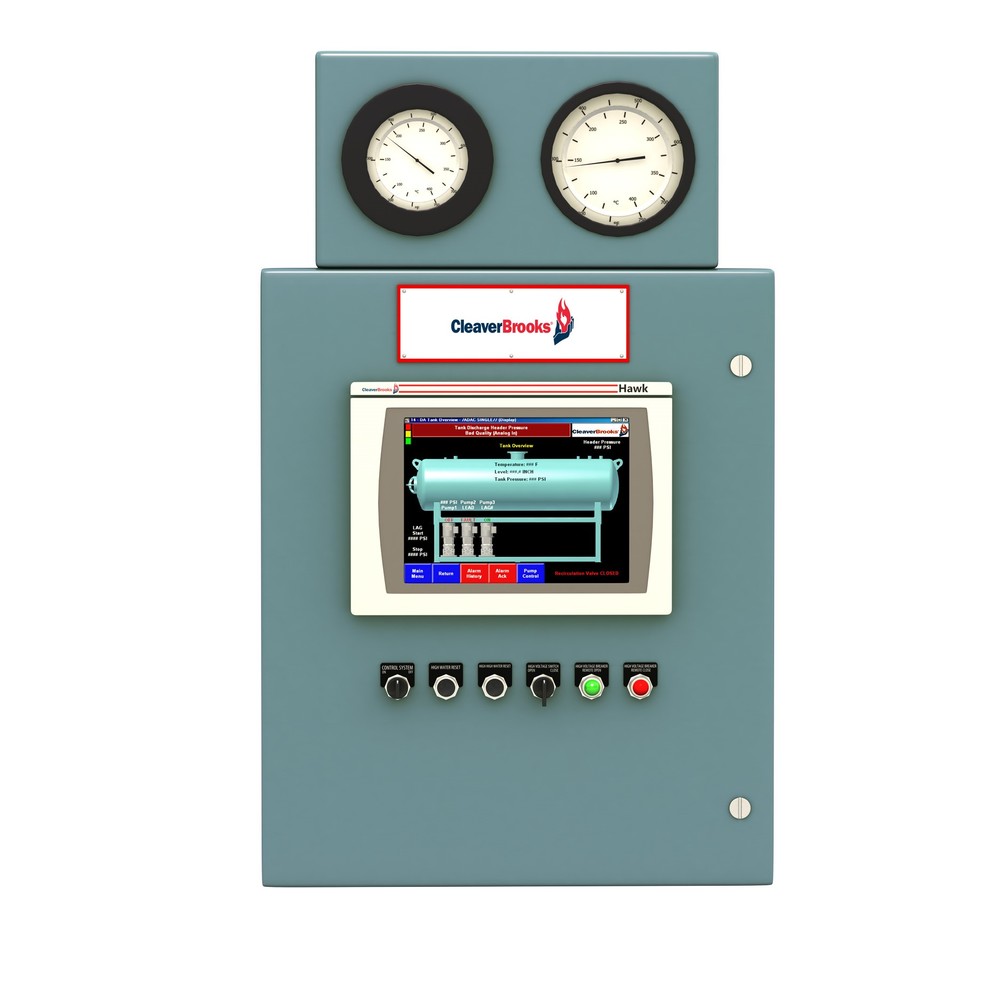
- Steam applications
- Lead-lag or one-pump-per-boiler control
- Variable speed drive or on-off pump control
- Maintains water level
- Single- or duo-tank system
- Advanced deaerator control system
- Complete deaerator control and monitoring
- Allen-Bradley PLC based hardware allows for custom programming
- Flexibility and custom applications including: High Pressure Condensate Receivers (HPCR) High Pressure Deaerators (HPDA)
- Communication to BAS
- On-off or variable speed drive control of feedwater and transferpumps
- Control of various in/out and output control valves
The ADAC is a PLC-based deaerator and surge tank control system designed to optimize the delivery of feedwater to the boiler ensuring steam reliability and higher operating efficiency. It can monitor and control all points on a deaerator or surge tank and be adapted for the many different boiler systems in modern steam plants. The ADAC provides pump control via on/off or variable speed drives, functions as overall tank controls by monitoring and adjusting multiple input valves, condensate return, fresh water make-up, and emergency make-up to maintain consistent water level without overflowing. The ADAC also controls the steam pressure to properly maintain water temperatures and ensures water quality is maintained, extending the life of your boiler. It can communicate data to most BAS systems and/or the C-B Master Panel. The ADAC’s interface puts the control of the deaerator or surge tank at your fingertips with its user-friendly menu system and screens.
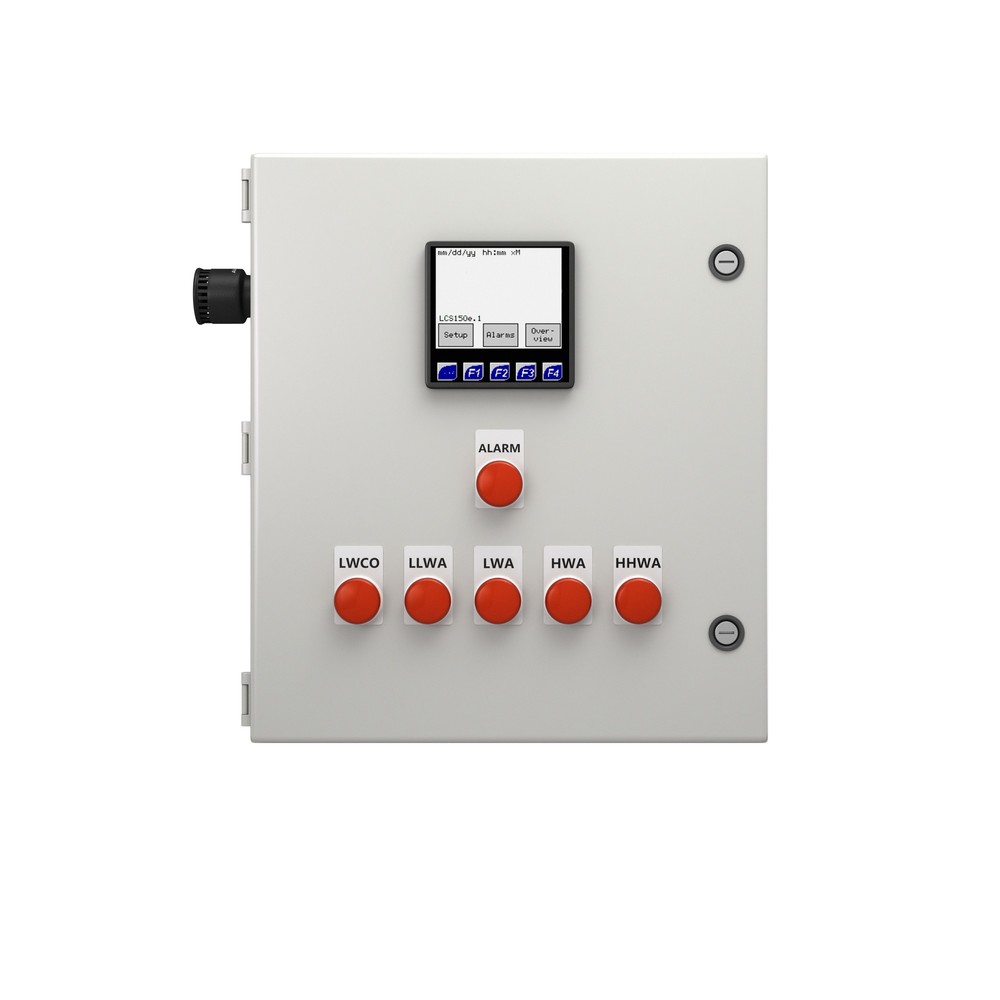
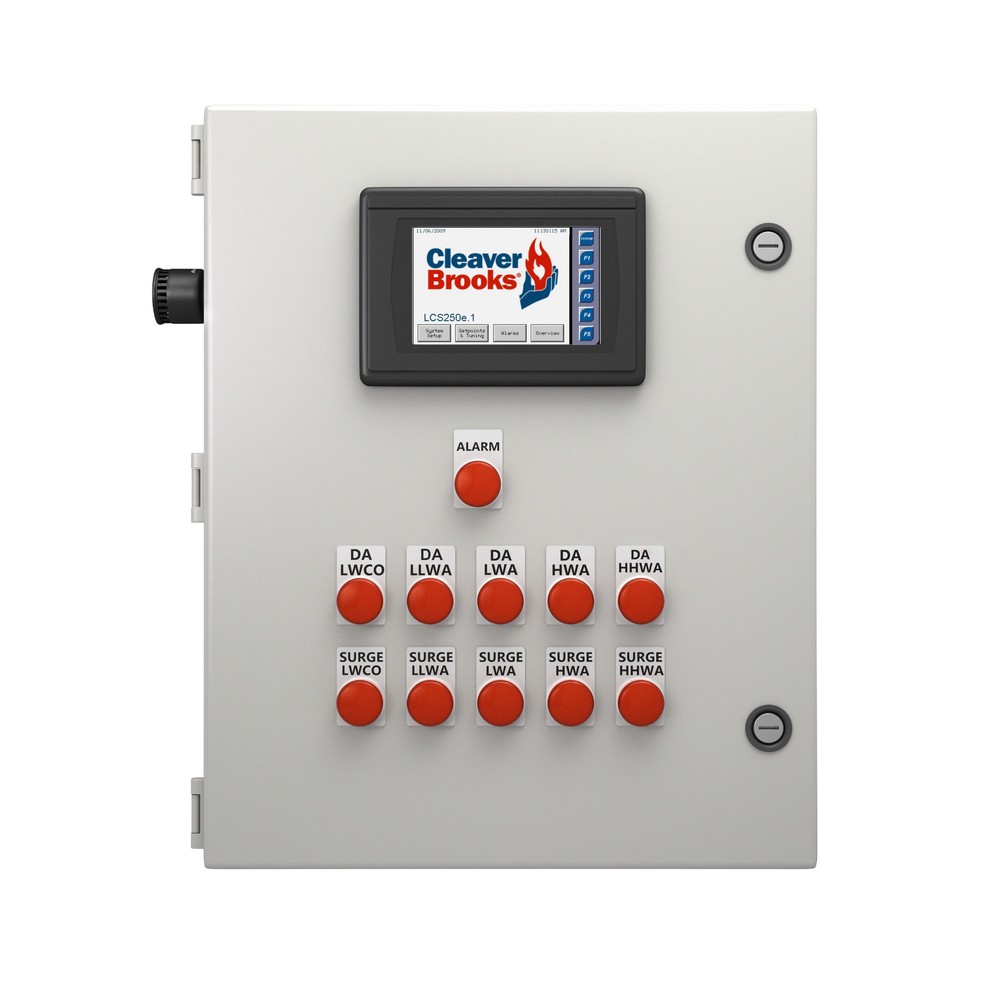
- Pressurized or atmospheric tank level control
- Configurable electronic control
- 1 to 2 modulating valves
- Maintains water level
- Single-tank system with LCS150 and a two-tank system with LCS250
- Single level-control system
- PLC controlled
- Modbus communications
- Data logging to optional Micro SD card
- User-selectable set points
The LCS control system was designed to provide easy level control for deaerators and atmospheric surge or condensate tanks. By utilizing a simple PLC platform, the LCS is configurable to adapt to a number of different system configurations. The LCS250 offers two-tank level control. Single Tank Level Control: The LCS 150 system accepts a 4-20 mA input for use as a level signal. Data is available via Modbus RTU communications or logged to an optional Micro SD card. Setup and control are easy with the LCS150’s interface user-friendly menu system and setup screens. The LCS is a great entry-level control system, and is ideal in situations where electronic level control is preferred over mechanical level control.
The LCS 250 is used when level control is provided for the deaerator tank while the surge tank receives feed control, with a bias to limit the valve position according to surge tank level. The system accepts a 4-20 mA input signal from each of the deaerator and surge level transmitters. Data is available via Modbus RTU communications or logged to an optional Micro SD card. The LCS250’s interface puts the control of the level control of a single tank deaerator and surge system at your fingertips with its user-friendly menu system and screens.
- Two tank level-control system
- PLC controlled
- Modbus communications
- Data logging to optional Micro SD card
- User-selectable set points
- The LCS250 is a great entry-level control system, and is ideal in situations where electronic level control is preferred over mechanical level control in a two-tank system.
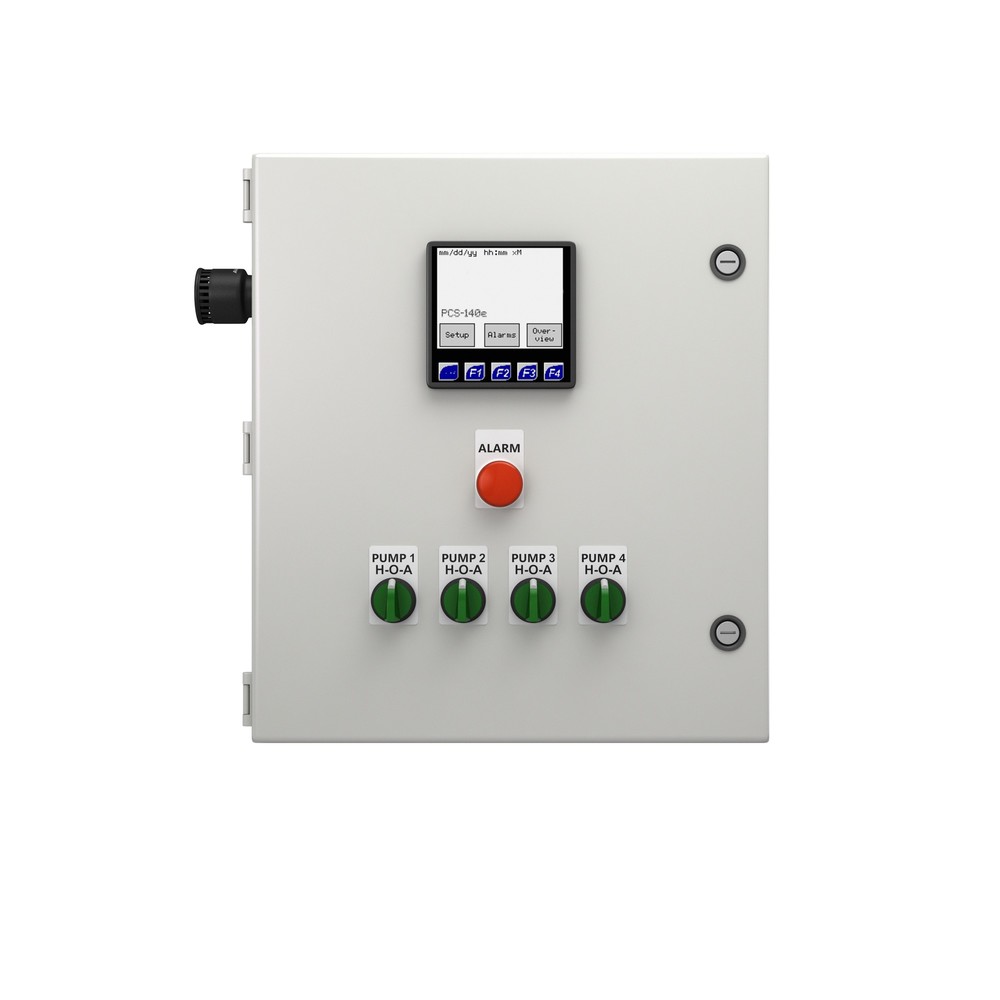
- ump control system
- Individual pump control up to four pumps
- Electronic control
- Lead/lag sequencing
- On/off or variable speed drive pump control
- Pump lead/lag on timed rotation
- On/off or variable speed pump control of up to 4 pumps
- PLC controlled
- Modbus RTU communications
- Data logging to optional Micro SD card
- User-selectable set points
The PCS is a simple pump control system with lead/lag sequencing on a timed rotation, “first on first off” basis, or manual rotation (user-selectable). Pumps are turned on or off as required to maintain a pressure set point within a user-configurable deadband. The PCS can control from 2 to 4 pumps for either on-off or VSD control. Data is available via Modbus RTU communications or logged to an optional Micro SD card.